This article is available in English too.
Carburo, carburo di tungsteno, metallo duro, carburo cementato e molti altri marchi registrati sono spesso utilizzati indifferentemente per indicare un materiale molto diffuso per la produzione di utensili.
Per essere precisi, questi termini non sono esattamente intercambiabili.
Il metallo duro, o carburo cementato, si riferisce a una classe di materiali costituiti da particelle di carburo disperse all'interno di una matrice metallica. Nella maggior parte dei casi, il carburo scelto è il carburo di tungsteno, ma possono essere aggiunti altri elementi formanti carburi, come il tantalio (sotto forma di TaC) o il titanio (sotto forma di TiC).
La matrice metallica, spesso definita "binder" (da non confondere con la cera e i polimeri tipicamente utilizzati nella metallurgia delle polveri), è solitamente costituita da cobalto, ma vengono utilizzati anche nichel e cromo. Questa matrice agisce come un "cemento", tenendo insieme le particelle di carburo (da qui la definizione "carburo cementato").
Per formare il metallo duro, le polveri di carburo vengono macinate con il legante metallico per ottenere una polvere che viene consolidata mediante pressatura, estrusione o stampaggio a iniezione di metallo (“Metal Injection Molding”, MIM), seguito da sinterizzazione.
In questo senso, il carburo cementato non è un metallo ma, più propriamente, un materiale composito.
Se nella composizione prevale il carburo di titanio invece del carburo di tungsteno, si forma un materiale diverso chiamato "cermet".
Se i componenti vengono fusi e legati invece di essere sinterizzati, si forma la stellite, una lega di cobalto-cromo contenente tungsteno e molibdeno.
Ora che abbiamo definito il carburo cementato, diamo un'occhiata più in dettaglio al suo processo di produzione, alle sue applicazioni e al modo in cui i forni in vuoto svolgono un ruolo essenziale in questo senso.
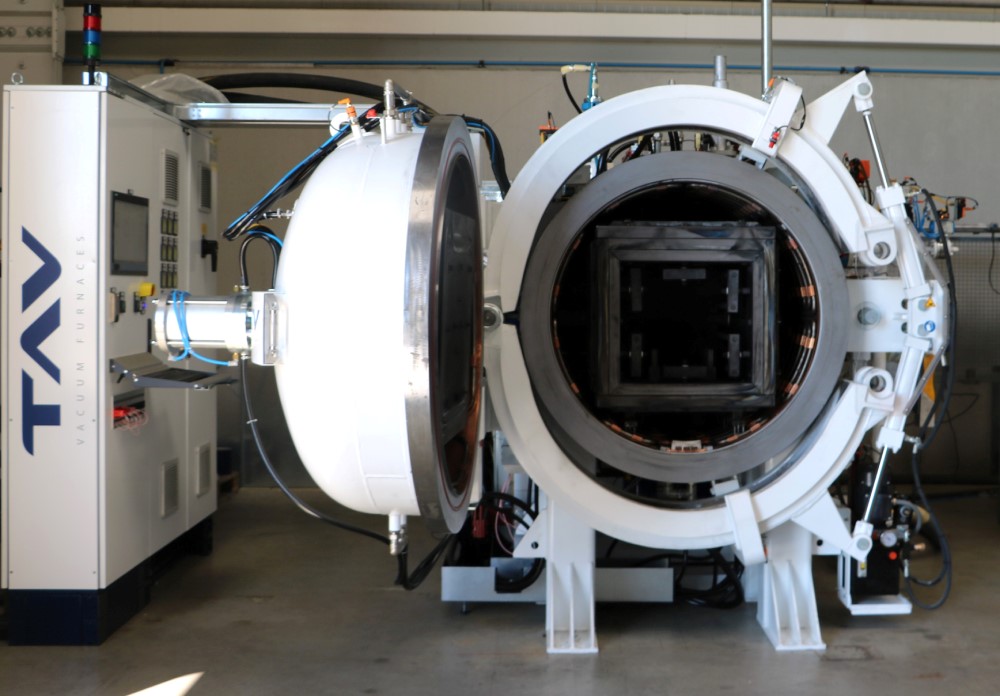
TAV VACUUM FURNACES HM Series - Sinter-HIP Furnace
Polveri ed Applicazioni
Per produrre le polveri di partenza, la polvere di tungsteno viene carburata con diversi metodi per ottenere il WC, quindi macinata insieme al binder metallico e, eventualmente, ad altri carburi.
Nella loro composizione tipica, queste polveri di partenza contengono tra il 70% e il 97% di carburi di tungsteno, mentre i carburi di titanio e tantalio possono essere presenti tra lo 0,5% e il 20%.
Il contenuto di cobalto nei composti commerciali varia tra il 3% e il 25%. A volte, per applicazioni specifiche, si preferiscono altri leganti metallici; i sistemi WC-Ni e WC-Ni-Cr, ad esempio, non sono magnetici (a differenza del WC-Co) e sono preferiti quando è richiesta un'elevata resistenza alla corrosione.
Per formare la cosiddetta "green parts” (un pezzo fatto di materiale in polvere, già modellato ma non ancora sinterizzato) le polveri di partenza vengono compattate con tecniche diverse, a seconda delle dimensioni e della complessità del pezzo: pressatura a freddo ed a caldo, estrusione o stampaggio a iniezione di metallo (MIM).
In tutte le tecniche citate viene aggiunta una frazione di cera o di lubrificante per consentire lo scorrimento delle particelle di polvere durante la pressatura e garantire la necessaria resistenza ai pezzi verdi da manipolare. Questa frazione può essere molto bassa, ad esempio per lo stampaggio a caldo, o significativa, fino al 7-8% in peso; è questo il caso del MIM.
Anche se non esiste un metodo di classificazione universalmente accettato per il carburo cementato, di solito vengono definite diverse composizioni in base alla loro applicazione. Secondo le norme ISO, il carburo cementato per utensili è suddiviso in categorie (K, P, M e, più recentemente, N, S, H) e sottogruppi chiamati gradi, denominati da numeri crescenti in base al contenuto di cobalto. Ogni grado è specifico per un determinato materiale del pezzo, metodo di lavorazione e condizione di lavoro. A ogni grado è associata una particolare granulometria.
La dimensione dei grani varia solitamente da 0,2 μm (“nano”) a 8 μm (“extra coarse”).
Oltre alla composizione dei carburi, il contenuto di cobalto e la dimensione dei grani sono i parametri principali che influenzano le proprietà meccaniche del carburo cementato.
In generale, la tenacità migliora mentre la durezza e la resistenza all'usura diminuiscono con l'aumentare del contenuto di cobalto. D'altra parte, per un certo livello di cobalto, la durezza migliora con la diminuzione della dimensione dei grani di WC. Nella tabella seguente sono riportati alcuni esempi di composizione per alcune applicazioni di lavorazione tipiche.
Classificazione
ISO
|
Co
(peso %)
|
TiC (peso %)
|
TaC (peso %)
|
VC (peso %)
|
Cr (peso %)
|
Dimensione
Grani
|
Durezza
(HRA)
|
Grado
|
Applicazioni
Tipiche
|
K01
|
5.5
|
/
|
0.7
|
/
|
/
|
Fine
|
92.4
|
“Straight”
|
Tornitura, Fresatura, Foratura Ghisa
|
K20
|
6
|
0.17
|
0.34
|
/
|
/
|
Fine
|
92.0
|
“Straight”
|
Tornitura, Fresatura, Foratura Ghisa
|
K30
|
11
|
0.4
|
0.8
|
/
|
/
|
Media
|
89.7
|
“Straight”
|
Tornitura, Fresatura, Piallatura Ghisa
|
M10
|
6
|
/
|
/
|
0.2
|
0.3
|
Extra Fine
|
92.8
|
“Micrograin”
|
Tornitura, Fresatura, Foratura Superleghe
|
M25
|
10
|
/
|
/
|
0.3
|
0.5
|
Extra Fine
|
91.9
|
“Micrograin”
|
Tornitura, Fresatura, Foratura Superleghe
|
P15
|
5.5
|
3
|
4.5
|
/
|
/
|
Media
|
91.4
|
“Alloyed”
|
Tornitura, Fresatura, Piallatura Acciai
|
P30
|
10
|
6.5
|
11.4
|
/
|
/
|
Media
|
91.2
|
“Alloyed”
|
Tornitura, Fresatura, Piallatura Acciai
|
P45
|
11
|
5.5
|
3.5
|
/
|
/
|
Media
|
90.5
|
“Alloyed”
|
Tornitura, Fresatura, Piallatura Acciai
|
Dopo la compattazione della polvere, i pezzi sono pronti per la sinterizzazione, necessaria per consolidare la polvere di partenza in pezzi ad alta densità.
Deceratura
La prima fase del processo di consolidamento è sempre la deceratura. Come già detto, le “green parts” di carburo cementato contengono una certa quantità di cera/lubrificante, spesso paraffina o PEG, che deve essere rimossa prima di riscaldare i pezzi alla temperatura di sinterizzazione. Una deceratura incompleta prima della sinterizzazione può portare alla formazione di porosità da gas intrappolati, derivanti dall'evoluzione dei vapori di cera all'interno dei pezzi, e di residui carboniosi.
Potrebbe essere controintuitivo quando si parla di carburi, ma un eccesso di carbonio libero all'interno della matrice di carburo cementato è gravemente dannoso per le sue proprietà. Il sistema tungsteno-carbonio-cobalto esiste infatti solo quando questi elementi hanno proporzioni ben definite; troppo carbonio formerà grafite (porosità da carbonio), troppo poco carbonio formerà l'indesiderata fase η. Per questo motivo, il controllo dell'atmosfera di deceratura e del profilo termico è fondamentale per garantire la completa rimozione del legante a una temperatura adeguatamente bassa, al di sotto del punto di "cracking", evitando sia la carburazione che la decarburazione dei pezzi.
A seconda delle proprietà chimiche e fisiche della cera, soprattutto del suo punto di fusione, punto di ebollizione e pressione di vapore, si possono applicare diversi metodi di deceratura, tra cui la deceratura in pressione parziale con alcuni millibar di gas o la deceratura in sovrapressione, a pressione leggermente superiore rispetto a quella atmosferica. In entrambi i casi, come gas di processo si utilizzano argon o idrogeno. Per i pezzi MIM, che contengono percentuali più elevate e sistemi di cera-polimero più complessi, si applica solitamente una fase di deceratura con solvente prima della deceratura termica.
È necessario utilizzare adeguati sistemi di intrappolamento della cera; per proteggere le pompe da vuoto da contaminazioni nel caso di deceratura in pressione parziale, oppure per condensare la maggior parte dei composti organici volatili prima che possano raggiungere il postcombustore all'uscita del forno nel caso di deceratura in sovrapressione. Inoltre, è possibile applicare una camicia riscaldata al tubo che collega il forno alla trappola raffreddata, per evitare la condensazione della cera prima dell'ingresso della trappola e l'ostruzione del tubo nel lungo termine.
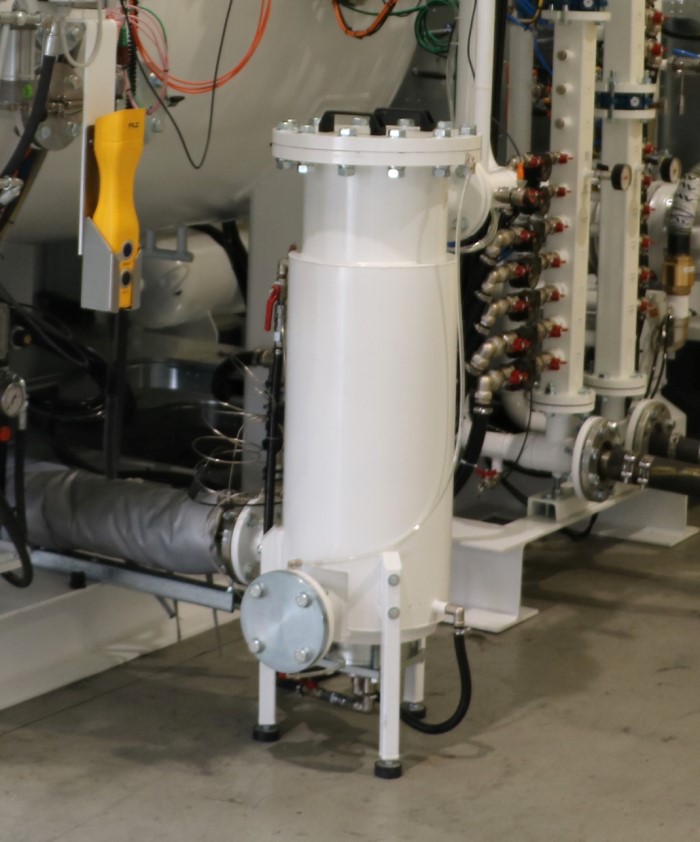
TAV VACUUM FURNACES trappola per cera raffreddata
I forni che operano in sovrappressione con l'idrogeno richiedono sistemi e sicurezze supplementari, tra cui un postcombustore elettrico o a gas per evitare l'accumulo di idrogeno in un'area confinata.
Inoltre, in TAV VACUUM FURNACES utilizziamo la nostra tecnologia DST (Double Sealing Technology) sui forni a idrogeno per eliminare completamente qualsiasi possibilità di perdite su tutte le flange, compresa la porta. Infine, un PLC di sicurezza e una strumentazione ridondante assicurano che tutti i parametri rilevanti siano all'interno dei livelli operativi di sicurezza.
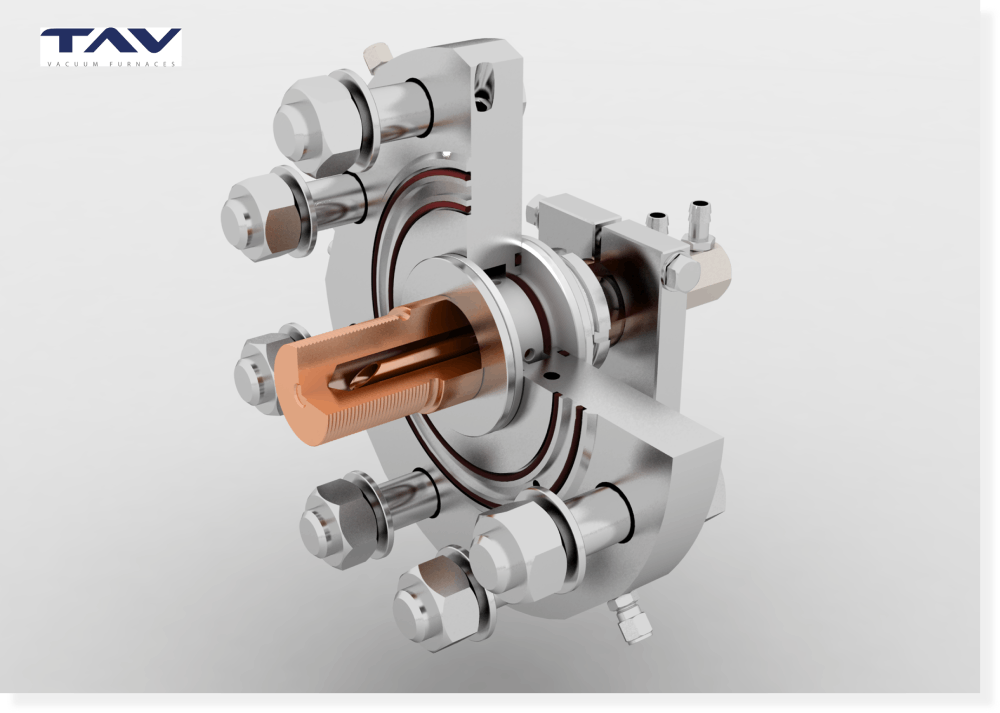
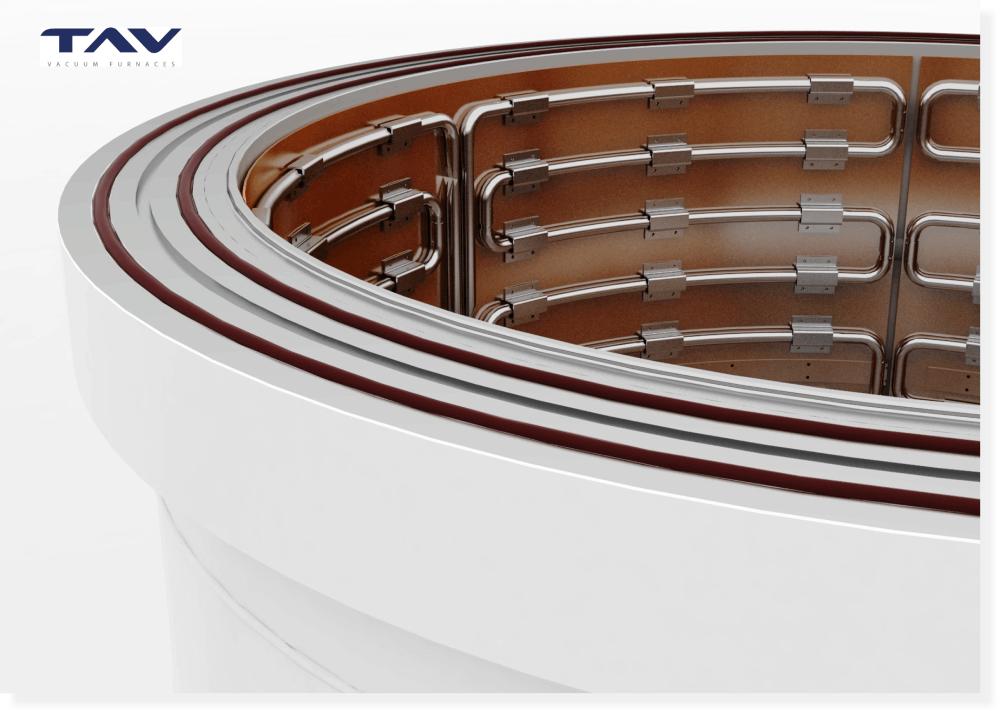
TAV VACUUM FURNACES DST (Double Sealing Technology)
Non perdetevi la seconda parte dell'articolo, in cui parleremo della sinterizzazione in vuoto e della sinterizzazione-HIP del carburo cementato, nonché delle attrezzature dedicate a questi processi!