In this article, I will talk about Additive Manufacturing and
in this case Selective Laser Melting (SLM). In particular, the
theme will focus on the role played by vacuum heat treatments in producing highly
reliable components, i.e. characterized by a better quality of the material and
an excellent fatigue resistance.
We will conclude by exposing the interesting experimental results obtained in
laboratory, thanks to a fruitful collaboration with the
University of Parma.
AM technology
Starting from a digital file and printing metal objects in 3 dimensions is no
longer a science fiction novel technology, but a reality possible with the
Additive Manufacturing.
Starting from a 3D design, it is possible to make metal components
with remarkable mechanical strength that can be used in various sectors, from medical
to aerospace. Thanks to Selective Laser Melting (SLM),
the creation takes place using a powder bed and a high power laser source, all controlled
in real time by a computer.
The role of the vacuum furnace in additive manufacturing
One of the tools to ensure that with this technology functional components can
be realized for the concrete application are the vacuum furnaces;
indeed, after the additive manufacturing process, heat treatments
or surface mechanical finish treatments are fundamental.
Vacuum furnaces are therefore essential for post-process treatments and are suitable
for processing a variety of materials, such as stainless steels,
titanium superalloys, cobalt-chromium alloys and
nickel superalloys.
Why heat treating under vacuum?
The products made by 3D printing are near-net-shape, in the
sense that selective melting (SLM) yields a lower production rate than other conventional
technologies, making it possible to obtain a more detailed component with more complex
forms, with less material, which otherwise would be almost impossible to obtain.
The passage inside a vacuum furnace therefore appears to be of considerable importance,
as it is characterized by the absence of oxygen and special diffusion pumps which,
through precise temperature control, determine the desired vacuum conditions. The
lack of oxygen is fundamental for medical and aerospace applications, for which
oxide contamination must absolutely be avoided.
The vacuum heat treatments are different depending on the considered additive
technologies.
Specifically, the heat treatments of
debiding and sintering are
indicated for the technologies of Fused Filament Fabrication (FFF) and
of Binder Jetting,
while the treatments of stress relieving and/or solubilization
are carried out for the Selective Laser Melting (SLM) technology.
What makes a vacuum furnace ideal for treating near-net-shape products?
Continue reading and find out which are the 3 critical points to keep under control
in Selective Laser Melting.
Did you like this article up to here?
Before you continue, follow us on our Twitter page pressing the button here below!
In this way, we'll be able to keep you updated on most advanced technologies for heat treatments not only with our posts, but also with the best articles that we collect around the web.
Additive manufacturing: laboratory results
In order to make the research on heat treatments more effective, we have set
up a special laboratory in which we have installed an all‑metal vacuum furnace
H3 and with which various types of tests have been carried out (hardening,
stress relieving, annealing, sintering, tempering,
etc.). Moreover, in the same laboratory a machine for the deposition of PVD coatings
with rotating cathodes has been positioned for a better surface finish of the samples
made using additive technologies.
The results obtained from the analysis carried out in the TAV laboratory were
aimed at:
- obtain a know-how in vacuum treatments and in the production of the relevant
furnaces to support companies, universities and research centers;
- take part in partnerships and research projects for the development of these
and other emerging technologies;
- prepare and publish scientific information texts.
The Collaboration with the University of Parma
One of the most recent activities developed by TAV VACUUM FURNACES is a collaboration
with the University of Parma
on the topic of optimal fatigue resistance of specimens made with SLM technology.
Fatigue is one of the most significant and complex parameters of industrial components;
in the aeronautical field, in fact, fatigue is counted as the cause of a high percentage
of breakages and it is for this reason that the focus of the study has focused on
it in particular.
The objectives of the collaboration were as follows:
- determining the behavior of fatigue resistance at high rpm on samples made
with AM technology;
- evaluate the effects of vacuum heat treatment on the fatigue strength of
SLM components;
- consider the impact of anisotropy of SLM components on fatigue resistance.
Fatigue performance of the components
That of Additive Manufacturing SLM is a process that presents three fundamental
critical issues, which concern:
- the quality of the material in terms of metallographic microstructures;
- surface roughness;
- the process residues present on the final component.
To obtain the experimental results that I will show you shortly, specimens were
used in alpha/beta titanium superalloy (Ti-6Al-4V). The choice
of this material was not accidental; it is a particularly light alloy, but resistant
to corrosion and high temperatures. These characteristics make it the most suitable
material for automotive, aerospace and biomedical engineering applications.
The research was carried out through the use of standard samples with different
mechanical finishes and at a later stage, these were subjected to rotary bending
tests for measuring fatigue resistance.
Looking at the graph below, you can see that as the mechanical surface finish
increases, the fatigue resistance is also increased.
The two curves of the same color indicate that, with the same surface finish,
the two standard samples were increased in two different orthogonal directions with
respect to the plane on which the piece was built; the specimens therefore assumed
a different behavior depending on the direction of growth and this demonstrates
the relevance of the intrinsic anisotropic characteristic of the SLM technology.
In the second graph, you can see the effect of heat treatment on some samples,
indicated with red color curves. The trend of the curves shows that heat-treated
specimens exhibit better behavior in terms of fatigue performance, compared
to untreated ones.
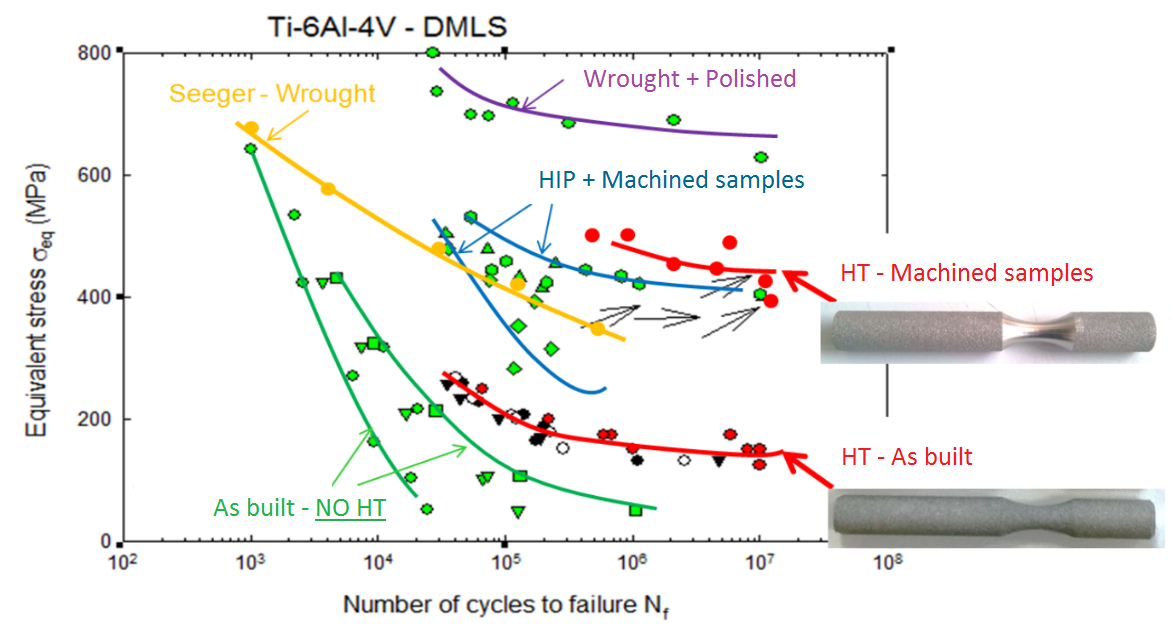
Conclusions
Additive Manufacturing it is undeniably the emerging technology
in the field of engineering. The realization of components destined for strategic
sectors requires processes and machinery that make a finished product and it is
able to withstand the stresses deriving from the application in the field.
We have shown in the laboratory that vacuum furnaces represent a highly functional
tool for performing post-heat treatment processes at Selective Laser Melting:
the passage inside a vacuum furnace determines improvements in the microstructure
of the material in terms of detensioning, isotropic behavior and surface roughness.
If you are interested in learning more, I invite you to read the article by Prof.
Nicoletto of the Department of Industrial Engineering of the University of Parma:
Metal additive manufacturing
and vacuum heat treatments.
Did you like the article?
Subscribe to our Telegram channel and stay up to date on most advanced technologies for heat treatments.
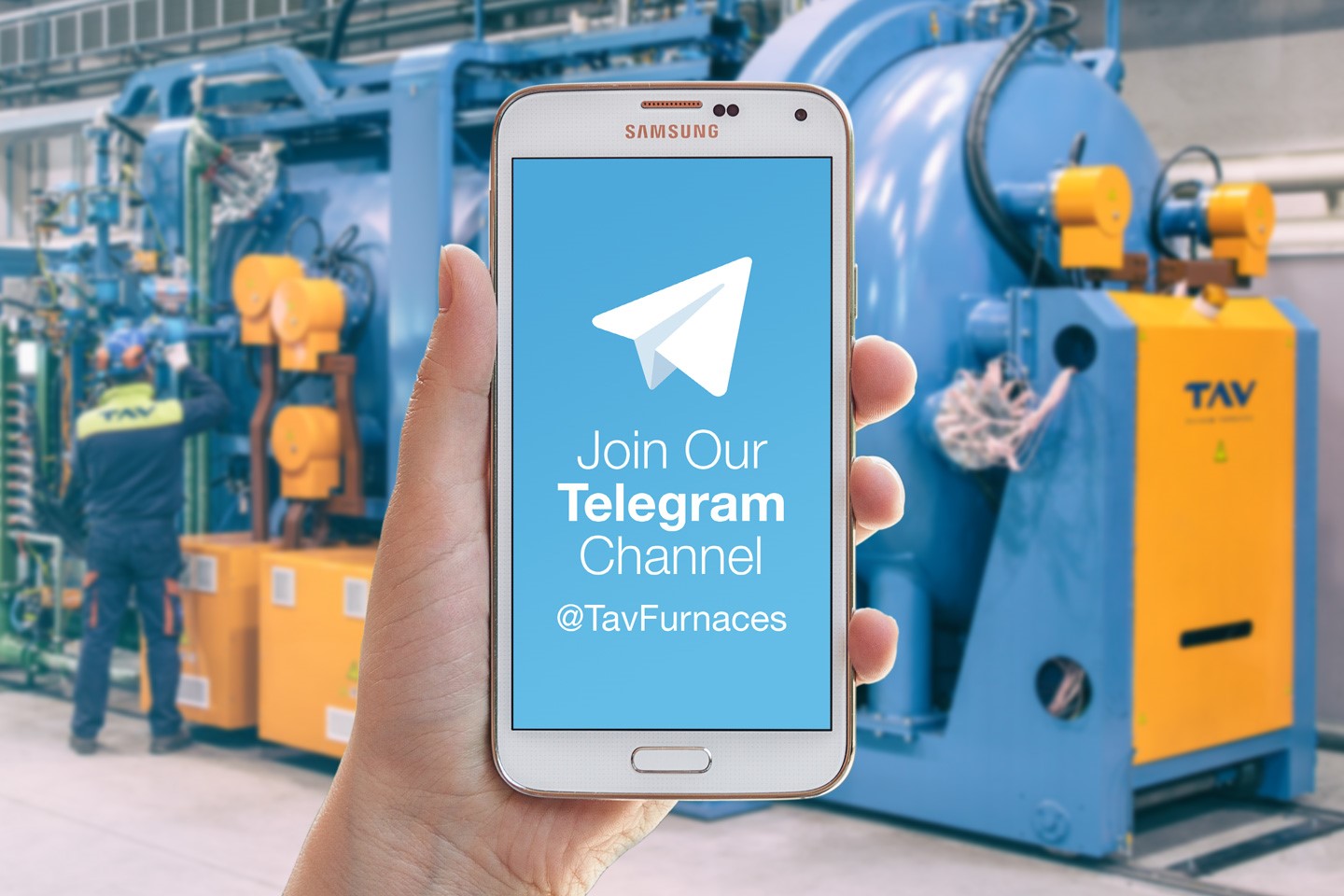
Don't you have Telegram?
If you do not have Telegram yet, use one of the following buttons to install it:
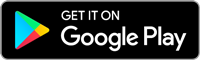
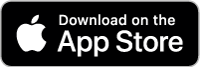