Effect of pre and post heat treatments on microstructure and adhesion of AlTiN films deposited on additive manufactured Ti-6Al-4V alloy.
On November 24 – 25, after one year of stop due to the COVID-19 pandemic, the 2021 edition of the ATZK CONFERENCE ON HEAT TREATMENT OF METAL MATERIALS IN MODERN INDUSTRY was held in Jihlava, Czech Republic.
During the events, several experts from the heat treatment industry and from Czech Universities shared their knowledge regarding conventional and vacuum heat treatments, equipment and new technologies for heat treatment of metals, surface heat treatments and coatings, heat treatment of additive manufacturing parts and many more industry-related topics.
Being one of the key market players in the vacuum furnaces industry, TAV VACUUM FURNACES also partecipated in the event helding a lecture during the first day of the event.
Our speech, in particular, covered the topic of the “Effect of pre and post heat treatments on microstructure and adhesion of AlTiN films deposited on additive manufactured Ti-6Al-4V alloy”.
The aim of this work, developed in collaboration with the unit of Lecco and unit of Padova of CNR ICMATE (National Research Council; Institute of Condensed Matter Chemistry and Technologies for Energy) was to investigate how vacuum heat treatments could affect and optimize the mechanical properties of coatings (in that case AlTIN coating) deposited through HiPIMS on titanium grade 5 parts printed via Selective Laser Melting.
But let’s proceed step by step and see what our lecture was all about.
What’s “Selective Laser Melting”?
The samples that served as substrates for the coatings in the experimentation were produced using a commercial Selective Laser Melting system.
Selective Laser Melting (SLM) is an additive manufacturing technology that makes use of a focused laser beam to melt a thin layer of metal powder.
The controller of a SLM system is able to guide the laser beam and selectively melt the material (in that case Ti-6Al-4V titanium alloy) according to a CAD file.
The repetition of this process layer after layer allow to produce a complete 3D part.
Thanks to the ability of producing fully dense parts with complex shapes, the high process flexibility and the possibility of processing a wide range of materials (e.g. steel, titanium alloys, NiCr and CoCr based alloys), SLM has quickly become the most popular AM technology, with a total of almost 10.000 SLM printer sold all over the world.
SLM printed parts, however, require post process heat treatment both to relieve residual stresses (arising from the rapid sequence of heat-up and cool-down phases occuring during the powder melting) and to optimize mechanical properties of the parts both in terms of strength and toughness.
The HiPiMS process
In the experimentation the substrates were coated using an HiPiMS system.
HiPiMS stands for High-power impulse magnetron sputtering and represent an evolution of the conventional PVD magnetron sputtering technique.
In general, PVD magnetron sputtering consists in the coating of a substrate through the ejection of material from a solid target source.
This process, as the name suggests, take adventage of the sputtering phenomenon to deposit a thin film onto the substrate.
In the case of HiPiMS, short, high energy impulses are adopted for the sputtering of the target.
Those impulses are able to generate an high degree of ionisation of the sputtered material that can be then directed applying an electrical bias to the substrate. This allow to obtain high quality, homogeneous coatings with an high density also on complex shaped parts.
On the other hand, deposition rate for HiPiMS is usually lower compared to direct current magnetron sputtering.
The benefits of AlTiN hard coatings
AlTIN (Aluminum Titanium Nitride) are hard coatings, i.e. coating aimed at improving the surface hardness and wear resistance of the coated part.
AlTiN coatings also allow for an exceptional oxidation resistance and thermal stability up to high temperature (up to 900°C) thank to the formation of an hard passive layer of Al2O3 and TiO2 mixed oxides.
Thickness of physical vapour deposited AlTiN thin layers is usually in the 1-4 µm range.
Thanks to their properties, AlTiN coating are particularly suited to increase service life of cutting tools and components in operations in harsh environment, for example for marine applications or in the oil and gas industry.
Experimental Procedure
The SLM printed samples used in the experimentation consisted in cylinders (24 mm in diameter, 5 mm in height) and in a simplified rotor produced from commercial Ti6Al4V powder.
To investigate the effect of the vacuum heat treatment on the AlTiN thin films deposited on the samples, heat treatment were carried out both prior and after the coating process.
The structure, the composition and the mechanical features of the realized thin films were investigated by Field Emission Scanning Electron Microscopy, Energy Dispersive Spectroscopy, scratch test and nanoindentation.
Heat Treatment
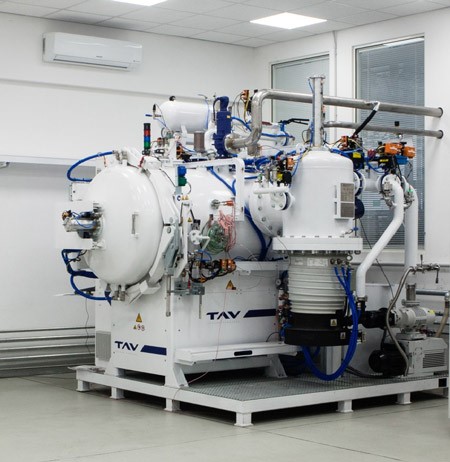
Figura 1: TAV TPH 30-30-45 HP all metal furnace
Heat treatment of the samples were carried out both prior and after the coating process at 720°C, 800°C and 950°C under high vacuum atmosphere (i.e. in a vacuum range between 1*10-5 mbar and 1*10-6 mbar) for 1 hour.
The temperatures of the thermal treatments carried out after the coating were selected in order not to exceed the ones used for treating the corresponding substrate.
All the heat treatments were performed in the TAV VACUUM FURNACES R&D Laboratory using our TAV TPH 30-30-45 HP.
This high vacuum furnace is equipped with an all-metal molybdenum hot zone and has the option of using pressurized argon gas to cool down the parts.
Moreover, the furnace is equipped with a dew point meter to check the gas purity. For these reasons, the TAV TPH 30-30-45 HP is well suited to heat treat materials that are both carbon and oxigen sensitive such as titanium.
Finally, with a maximum operating temperature of 1400°C degree, the furnace is able to cover the entire range of temperature adopted for stress relieving, annealing and aging of titanium alloys.
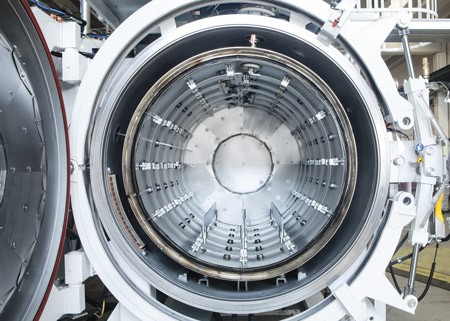
Figura 2: Hot zone of an All Metal TAV’s vacuum furnace
Coating
The protective thin films were deposited by reactive PVD HiPIMS onto Ti6Al4V disks (before and after vacuum thermal treatment). The deposition process was driven by a Ionautics Hipster 6 power supply maintaining constant power density (15 W cm-2), frequency (1500 Hz), pulse time (50 µs), substrate bias supplied by Ionautics Hipster 1 (-50 V power, frequency 1500 Hz, pulse time 100 µs, synchronized), temperature (350°C), and the substrate-target distance (60 mm).
Polishing of the substrates prior to coating was carried out using a colloidal silica suspension (OP-U, 0.04 µm, Struers) by using a Tegramin 20 automatic grinder (Struers).
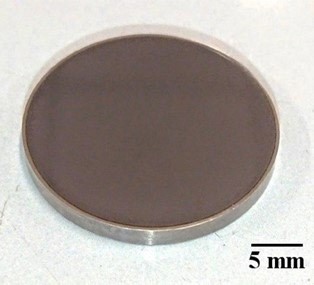
Figura 2: Ti-6Al-4V SLMed sample coated with the AlTIN thin film
Samples and Thin Films Analysis
The morphological and quantitative compositional characterizations were performed by Sigma Zeiss field emission scanning electron microscope (FE-SEM).
Three-dimensional topological characterization of surfaces was carried out by a stylus profiler (Bruker, Dektat XT).
The adhesion of AlTiN coatings deposited onto AMed substrates, polished and then subjected to vacuum thermal treatments, was analysed by UMT-2 tribotester (Bruker) equipped with a standard Rockwell C diamond tip. Test parameters were set following the EN 1071-3 standard for ceramic materials in Progressive Loading Scratch Test (PLST) mode. A minimum of 3 scratch marks were made for each coating to assess the repeatability.
Hardness and elastic modulus values were measured by instrumented nanoindentation, with Nanotest system (Micromaterials, Wrexham, UK) equipped with a Berkovich tip. Data were obtained by statistical analysis of 25 indentations for each.
Results
FE-SEM surface micrographs of the substrates confirmed the occurrence of the recrystallisation process particularly evident on the 950 °C treated sample where overlapping large and flat grains could be observed. Moreover, the sample treated at 800 °C showed a homogeneous mesoporous morphology.
Surface roughness also increased significantly with the temperature of the vacuum heat treatment.
Scratch test performed on the films after the coating of the heat-treated polished substrates proved that brittle fracture occurred in all AlTiN coatings, with the one deposited onto the substrate treated at 800 °C having the highest critical load of delamination.
Nanoindentation measurements carried out on films deposited on vacuum treated substrates and on films subjected to further vacuum treatments did not show any significant deterioration of mechanical properties on the coatings, except for coated samples treated at 950°C, where film cracking occurred during the treatment.
As a tridimensional prototype, a simplified rotor, obtained by SLM and vacuum thermal treated at 800°C, was coated with AlTiN without any previous polishing. The film resulted homogeneous, even if it showed poor adhesion in some points, likely due to the native surface morphology of the part given by SLM technique.
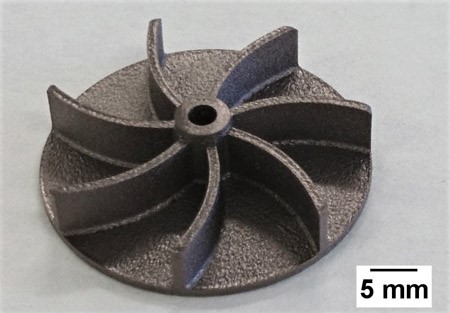
Figura 3: AlTiN coated SLMed simplified rotor
In conclusion
The study demonstrated that it is possible to coat the titanium alloy substrates with dense AlTiN films obtaining a good improvement of the mechanical surface features. Vacuum heat treatment of the SLMed parts proved to have an impact on the coating performace, with the treatment at 800°C resulting in improved thin film adhesion.
Moreover, the coating maintained substantially unaltered mechanical properties after further thermal treatments up to 950°C, temperature at which breaking of the coating can be observed.
To learn more about the coating process of additive manufactured Ti64 parts you can read our previous article (https://www.tav-vacuumfurnaces.com/blog/53/en/coating-titanium64-additive-manufacturing-1) where we discussed more in depth SLM printing and coating parameters and some preliminar results from this experimentation.
Also check out our article (https://www.tav-vacuumfurnaces.com/blog/50/en/heat-treating-additive-manufacturing?culture=en) to learn why heat treat additive manufactured metal parts.
For further details about the experimentation, you can find the full paper
“Battiston, S., Montagner, F., Zin, V., Barison, S., Fiorese, A., Gionda, A., ... & Armelao, L. (2021). Vacuum Thermal Treatments for Surface Engineering of Selective Laser Melted Ti6Al4V Alloy. Journal of Materials Engineering and Performance, 30(9), 6874-6880”
at this link: https://rdcu.be/cqFBA
S. Battiston, F. Montagner, V. Zin, and S. Barison, Institute of Condensed Matter Chemistry and Technologies for Energy, National Research Council of Italy, ICMATE-CNR, C.so Stati Uniti 4, 35127 Padua, Italy;
A. Fiorese, A. Gionda and G. Valsecchi, TAV VACUUM FURNACES SpA, Via dell’ Industria 11, 24043 Caravaggio, BG, Italy;
M. Rancan, Institute of Condensed Matter Chemistry and Technologies for Energy, National Research Council of Italy, ICMATE-CNR, via Marzolo 1, 35131 Padua, Italy;
F. Sordello and M. Minella, Department of Chemistry and Interdepartmental Centre for Nanostructured Interfaces and Surfaces (NIS), University of Turin, Via P. Giuria 5, 10125 Turin, Italy;
C.A. Biffi, J. Fiocchi, and A. Tuissi, Institute of Condensed Matter Chemistry and Technologies for Energy, National Research Council of Italy, ICMATE-CNR, Unit of Lecco, Via Previati 1/E, 23900 Lecco, Italy;
L. Armelao, Institute of Condensed Matter Chemistry and Technologies for Energy, National Research Council of Italy, ICMATE-CNR, via Marzolo 1, 35131 Padua, Italy; Department of Chemical Sciences and Materials Technologies, National Research Council of Italy, Piazzale A. Moro 7, 00185 Rome, Italy; and Department of Chemical Sciences, University of Padua, Via Marzolo 1, 35131 Padua, Italy