The minting industry has to be compliant to the highest level of standard certifications in order to avoid every possibility of falsification and, at the same time, to satisfy a high level of quality and reproducibility. The quantity of money and the great variety of coins in the world means that it is essential not make any sort of mistake in all the minting processes.
In the first part of this article we’ll take an interesting step-by-step look at the minting process, while in the second part we’ll discover the most optimized heat treatments for the minting industry.
How to obtain the master die
Let’s take a close-up look.
- Everything begins when a master craftsman designs a three-dimensional plaster model with 20 cm diameter of the positive image of the coin.
- The model is covered by a silicone rubber in order to make a mould.
- The artwork is reduced and cut into steel by a laser or pantograph and this is called master die.
The master die has the same diameter dimension and image of the coin: in this way, there are two steel master dies, one for every face of the coin.
The master die is then hardened and tempered to produce a positive tool called hob.
Note that the master die is not used to produce coins.
What do we need to produce our first coin?
The minting process
The working dies are obtained by pressing the master die design into another piece of soft steel.
From the master die several coining dies will be produced.
Two sets of dies are needed to strike a coin, one for the observe and the other for the revers.
The force used to strike the working dies with a hydraulic press is 160 tons of pressure: this is how the working dies have the negative image of the master die on their face.
To get the best results:
- the working dies must be hardened, tempered and machined to suit the coining press as well;
- at the end of the process dies must be textured, polished and Chrome Nitride plating takes place on the surface of the die, to reduce wear in the coining process and to extend the life of the dies;
- finally, blanks are cut from coils of metal alloy like a mixture of base copper covered by nickel.
Thus, the steel coin dies strike on blanks by plastic deformation with a hydraulic press.
This is the process through which working dies leave the positive image on the surface of coins we see every day.
It’s clear that the quality and definition of the steel dies is very important, since they have a fundamental role in the coining process.
Did you know that the working die usually strikes 12 coins per second?
For this reason the master and working dies must be compliant to standard UNI ISO 4957 for the cold working steels. The steel dies, in order to obtain a high level of reproducibility during the strike step, must be hard, tough, bright with a low level of wear.
How we can improve the mechanical properties of cold working steel die maintaining a very good definition of the surface at the same time?
Did you like this article up to here?
Before you continue, follow us on our Facebook page pressing the button here below!
In this way, we'll be able to keep you updated on most advanced technologies for heat treatments not only with our posts, but also with the best articles that we collect around the web.
The importance of vacuum heat treating
The vacuum heat treatment is the solution.
TAV VACUUM FURNACES has developed a special customized system in order to perform heat treatments maximizing the quenching effect during the hardening, guaranteeing simultaneously green standards and safety for the workers.
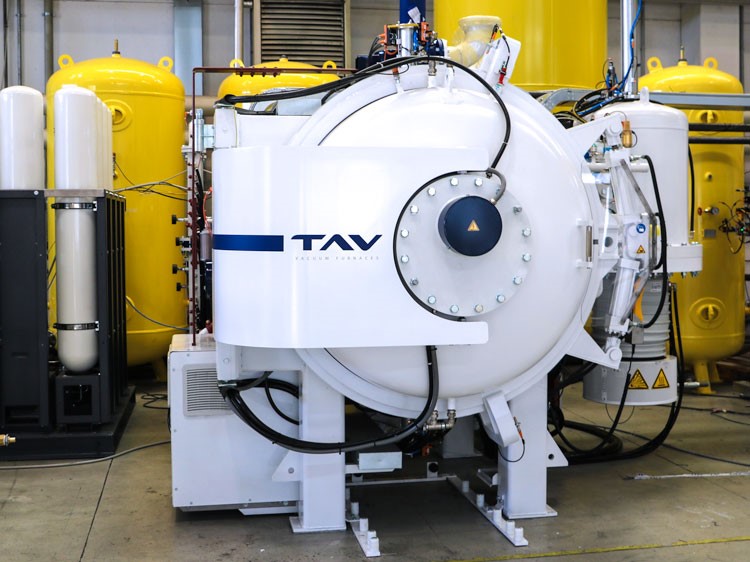
The vacuum furnace is equipped with a graphite hot chamber with mechanical and diffusion pumps so that it can reach a high level of vacuum, ultimate vacuum of 10-6 mbars.
It is possible to use a convection system up to 600 °C with inert gas.
This kind of furnace is used for the heat treatment necessary for the improvement of the cold working steel like coin dies, in a specific way:
- annealing treatment
- hardening treatment
- finally tempering in order to have coin dies hardness of 60-64 HRC.
How can we maximize the quenching process during the hardening treatment?
We can use helium inert gas during the cooling phase (as well as nitrogen gas).
Helium has a much better effect in the cooling step rather than nitrogen and so the hardening process is more effective.
Working for a green industry
But how can we afford the waste of helium and have an ecological approach?
A gas recovery system was developed in order to reduce the consumption of helium.
- Exhausted helium, used for a treatment, goes to a 5 stages compressor.
- The compressor is divided by the furnace with a mesh filter that avoids the passage of physical impurities. So, helium is compressed and passes through a separator.
In this way, there is a first coarse separation of helium by condensation.
After that, an anodized aluminium alloy filters out helium more accurately.
- Firstly, a molecular sieve separates helium from ppm of water, and an activated carbon divides the gas from the oil piston.
- Finally, the compressed gas will go to the helium tank in order to be recycled for another heat treatment.
In this way, we can recycle helium for new further treatments.
Working in a safe workspace
The last important feature to keep in mind is that we can carry out our treatment in a completely safe system. The control systems are for the temperature and pressure variables.
- For the temperature, we use the control, overtemperature and load thermocouples to detect the temperatures of furnace, vessel and load respectively.
- Moreover, there are detectors for overpressure and mechanical ring in order to avoid the possible opening of the frontal door and the manual latch.
Conclusions
TAV systems guarantee a high quality of the steel dies through vacuum technologies in order to improve the reproducibility and quality of the minting process. Furthermore, we always bear in mind the importance of green standards with our system of helium recycling in a completely safe condition for the workers.
Here below you can find all the slides we presented at The Coin Conference 2019.
Did you find this article useful?
If you think your friends will like it too, share it on Facebook.
You have only to press the button here below!