Nella vasta gamma di tecnologie di produzione additiva (Additive Manufacturing) oggi disponibili, il Binder Jetting si distingue per la capacità di combinare la flessibilità e la complessità delle parti tipiche dei processi di produzione additiva con un tasso di produttività ineguagliato da altre tecnologie AM.
Sviluppato da un brevetto del MIT dei primi anni '90, il Binder Jetting (BJT) è un processo a letto di polvere dove, contrariamente alle tecnologie di fusione a letto di polvere come SLM e EBM, il materiale viene compattato attraverso la deposizione selettiva di un legante liquido invece di essere fuso.
Ciò significa che il Binder Jetting è in grado di lavorare una vasta gamma di materiali, tra cui ceramiche e polimeri, anche se i riflettori negli ultimi anni sono stati certamente puntati sulla produzione di parti in metallo.
Per raggiungere la loro forza e densità finale, le parti stampate BJT in metallo si affidano poi alla sinterizzazione in un forno apposito.

Forno TAV MIM5 per deceraggio e sinterizzazione in vuoto
In questo articolo esamineremo il flusso di lavoro del Binder Jetting, lo confronteremo con altri processi di stampa 3D e di metallurgia delle polveri e discuteremo quali sono i vantaggi e i campi di applicazione di questa tecnologia.
Cos'è il Binder Jetting?
Il Binder Jetting consiste fondamentalmente nella deposizione selettiva di un legante liquido attraverso una testa di stampa, seguendo la "slice" (cioè la sezione 2D) di un file CAD. La piattaforma di costruzione si abbassa e un nuovo strato di polvere viene steso dalla racla. Il processo viene ripetuto strato dopo strato fino al completamento del build.

Flusso di lavoro per la produzione additiva Binder Jetting
La testa di stampa contiene centinaia di ugelli, il che significa che un alto volume di legante può essere depositato rapidamente mantenendo un'alta precisione e risoluzione dei pezzi.
Di solito, le parti BJT non hanno bisogno di supporti specifici poiché il pezzo è già sostenuto dalla polvere slegata presente all'interno del volume di costruzione.
Come già detto, il Binder Jetting è un "processo a freddo" perché non c'è fusione del materiale, e per questo motivo non c'è bisogno di preriscaldamento del letto di polvere per evitare cricche o distorsioni del pezzo, anche se il calore può essere applicato dopo la lavorazione di uno strato per accelerare l'asciugatura del legante.
Dopo la stampa, l'intero letto di polvere viene polimerizzato a bassa temperatura (circa 200°C) per asciugare ulteriormente e compattare la parte mentre è ancora circondata dalla polvere slegata.
Per le sue caratteristiche, questo processo potrebbe essere applicato virtualmente a qualsiasi polvere metallica, anche se sono presenti alcuni requisiti in termini di fluidità della polvere e distribuzione granulometrica per garantire una diffusione omogenea della polvere, una buona bagnabilità con il legante, una buona rugosità superficiale e una densità finale sufficientemente alta dei pezzi. Al momento, i metalli più comuni per la produzione a getto di legante metallico sono probabilmente l'acciaio inossidabile austenitico 316L e l'acciaio inossidabile martensitico 17-4 PH. Altri materiali qualificati disponibili dai produttori di macchine includono l'acciaio inossidabile 304L, Inconel 625 e Inconel 718, l'acciaio per utensili H13, D2 e M2, la lega di titanio Ti6Al4V e il rame.
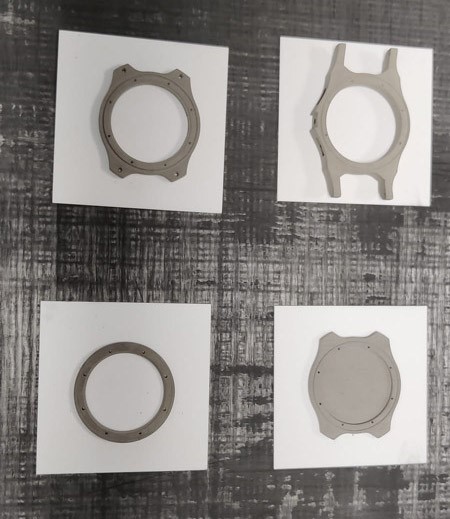
Componenti per orologi nello stato “green”, stampanti tramite ExOne X1 25PRO (su gentile concessione di Cor.Sa 3D)
Infine, dopo la fase di indurimento, il pezzo deve passare attraverso un ciclo di infiltrazione o sinterizzazione per raggiungere le sue proprietà meccaniche finali.
L'infiltrazione consiste nel densificare il pezzo attraverso l'introduzione di un materiale diverso che non deteriora le proprietà del metallo di base. Tipicamente, gli acciai vengono infiltrati utilizzando il rame, che penetra all'interno dei pori aperti permettendo di ottenere una buona densità finale.
Invece, l'unico modo per ottenere una parte metallica mono-lega resistente e densa è la sinterizzazione, cioè il mantenimento della parte a una temperatura adeguata per un tempo adeguato per promuovere la diffusione atomica tra le particelle di polvere e fonderle insieme.
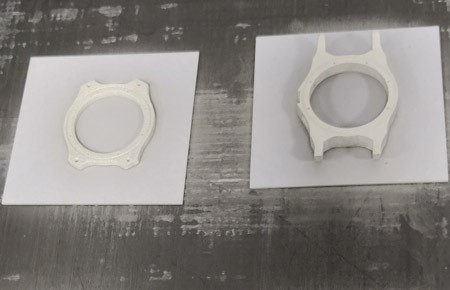
Componenti per orologi sinterizzati, stampati tramite ExOne X1 25PRO e sinterizzati nel forno TAV MIM3 (su gentile concessione di Cor.Sa 3D)
Trasformare pezzi belli in pezzi resistenti: il processo di sinterizzazione
I forni da sinterizzazione in vuoto sono di solito la scelta migliore per la sinterizzazione di parti Binder Jetting, grazie alla capacità di fornire parti sinterizzate brillanti e lucide, allo stretto controllo dei parametri di processo e alla possibilità di lavorare con diverse atmosfere di deceraggio e sinterizzazione.
I cicli di sinterizzazione per le parti BJT includono mantenimenti a bassa temperatura per bruciare tutti i residui di legante polimerizzati. Per i leganti liquidi organici usati tipicamente nel binder jetting, l'evaporazione inizia a circa 200°C e si completa prima che la temperatura del forno raggiunga i 500°C, anche se questo intervallo di temperatura può essere leggermente influenzato dall’ effettiva composizione del legante e dall'atmosfera di deceraggio. I parametri di deceraggio adeguati sono fondamentali per evitare cricche, deformazioni o la formazione di residui di legante a base di carbonio che porteranno alla diffusione del carbonio all'interno del pezzo, ostacolando la resistenza alla corrosione e peggiorando le proprietà finali del pezzo. Per la produzione di grandi volumi, è anche possibile eseguire questa fase in un forno da deceraggio dedicato, che aumenterà la produttività e faciliterà il processo di pulizia. In ogni caso, sia che si scelga di utilizzare forni separati per il deceraggio e la sinterizzazione o di eseguire l'intero processo in un unico forno da deceraggio e sinterizzazione, è importante che il forno sia dotato di un adeguato sistema di intrappolamento per evitare che il legante vaporizzato raggiunga le pompe da vuoto. Se volete saperne di più sul deceraggio e sulle caratteristiche di un forno da deceraggio all'avanguardia, consultate il nostro articolo su "COME DECERARE CORRETTAMENTE LE PARTI PRODOTTE CON LA MANIFATTURA ADDITIVA DEL METALLO".
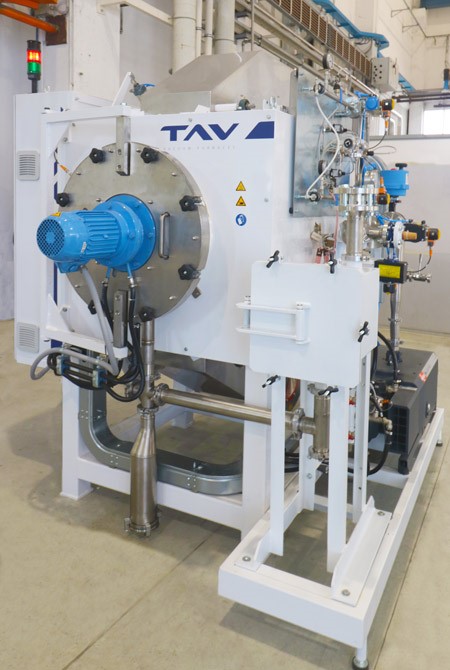
Forno per debinding TAV D3
I parametri di sinterizzazione (cioè tempo e temperatura) dovrebbero essere adattati al materiale e alle dimensioni della parte. Il ciclo di sinterizzazione dovrebbe anche includere dei mantenimenti a temperature intermedie e diverse velocità di riscaldamento per massimizzare l'omogeneità della temperatura sulla parte, minimizzando il tempo del ciclo. In generale, la maggior parte delle prassi provenienti dal Metal Injection Molding (MIM) riguardanti la sinterizzazione possono essere trasferite al Binder Jetting anche se effetti come il ritiro e le deformazioni devono essere tenuti in considerazione ancora più attentamente per le parti Binder Jetting poiché, questa tecnologia permette di produrre parti più grandi con una geometria più complessa. Inoltre, il diverso metodo di produzione non fa uso di pressione esterna durante la fase di formatura, portando a parti con una maggiore tendenza a perdere la forma durante la sinterizzazione. La sinterizzazione di parti BJT in forni a vuoto può essere effettuata con diverse atmosfere, tra cui:
- Il vuoto
- Azoto o Argon
- Miscele azoto/idrogeno o argon/idrogeno
- Idrogeno puro (sia a bassa pressione, sotto i 10 mbar, che in sovrapressione, leggermente sopra 1 bar)
La scelta dell'atmosfera di sinterizzazione deve essere adattata al materiale e alle proprietà desiderate del pezzo. Per avere maggiori informazioni sulla scelta dell'atmosfera di sinterizzazione, consultate il nostro articolo SINTERIZZAZIONE SOTTOVUOTO DI ACCIAI INOX: COME SCEGLIERE LA GIUSTA ATMOSFERA DI SINTERIZZAZIONE.
Sia i forni da sinterizzazione in vuoto con camera termica in grafite che quelli metallici sono adatti: la scelta dovrebbe essere fatta, ancora una volta, tenendo in considerazione il materiale del pezzo e le applicazioni finali. I forni da sinterizzazione in vuoto metallici sono la scelta migliore per i materiali sensibili all'ossigeno (come il titanio) e consentono una maggiore versatilità dei materiali da trattare. D'altra parte, i costi di investimento e di funzionamento sono a favore dei forni di sinterizzazione in vuoto in grafite. Inoltre, i forni da sinterizzazione in vuoto di solito includono una storta a più livelli, come il MIM-Box TAV che rappresenta lo stato dell’arte della tecnologia, per massimizzare la capacità di carico all'interno del volume utile. Analogamente a quanto discusso in precedenza per la camera termica del forno, anche il MIM-Box TAV è configurabile sia con struttura in grafite che in metallo refrattario. Se volete scoprire di più sulle differenze tra i forni di sinterizzazione in vuoto con camera termica in metallo ed in grafite, vi invitiamo a leggere la nostra GUIDA STEP BY STEP ALLA SINTERIZZAZIONE IN VUOTO.
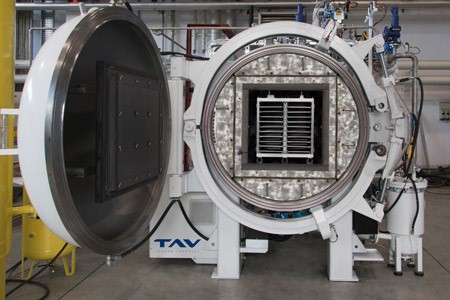
Camera termica e MIM-Box del forno TAV MIM5 per deceraggio e sinterizzazione in vuoto
L'industria del Binder Jetting oggi
Se consideriamo la sola produzione di componenti in metallo, al momento sono pochi i produttori di macchine Binder Jetting presenti sul mercato: ExOne, Digital Metal e Desktop Metal, anche se sia HP che GE Additive stanno sviluppando da tempo un sistema BJ che dovrebbe essere rilasciato in un prossimo futuro.
Le peculiarità del Binder Jetting lo rendono una tecnologia competitiva rispetto ad altri processi sia dentro che fuori il mondo dell'Additive Manufacturing.
La natura “strato per strato” del processo BJT gli permette di avere la stessa libertà di progettazione tipica dei processi Powder Bed Fusion. Rispetto ai processi PBF, il costo per pezzo quando si opera a regimi di produzione è sicuramente inferiore. Inoltre, essendo un processo "freddo", il BJT non induce tensioni residue all'interno del pezzo che richiedono un ulteriore trattamento termico, come nel caso del PBF. D'altra parte, l'ottimizzazione del processo di produzione Binder Jetting richiede non solo una buona conoscenza della fase di stampa, ma anche del post processing di deceraggio e sinterizzazione. Al momento, il numero di sistemi Binder Jetting installati nel mondo è relativamente molto inferiore a quello dei sistemi PBF, anche se la tecnologia esiste da più di due decenni. La maggiore diffusione dei sistemi PBF significa anche che sono disponibili molti studi su queste tecnologie, consentendo una comprensione più profonda del processo e dei parametri post processo. Infine, la presenza di standard pubblicati per i processi PBF ha certamente aiutato la crescita delle applicazioni sul campo per le parti PBF nell'industria aerospaziale, automobilistica e biomedicale, mentre le applicazioni delle parti BJT sono ancora per lo più limitate ai prodotti di consumo.
Il Metal Injection Molding (MIM) è senza dubbio il processo di metallurgia delle polveri più comune per la produzione di componenti di piccole e medie dimensioni. Il MIM permette di produrre pezzi in una vasta gamma di leghe metalliche (possiamo affermare che tutte le leghe metalliche che sono oggi disponibili per BJT fanno parte dell'industria MIM da molto tempo) con un'ottima risoluzione dei particolari e finitura superficiale. Tuttavia, il MIM ha alcune limitazioni sulla complessità del design legate all'impossibilità di stampare certe caratteristiche (cavità interne, sottosquadri, fori interni, spirali, spigoli vivi, ...). Inoltre, le macchine BJT di ultima generazione possono produrre pezzi di dimensioni maggiori rispetto a quelle tipiche dei componenti MIM, anche se i vincoli dimensionali per entrambe le tecnologie sono più legati alle attrezzature disponibili e alla sinterizzazione che al processo stesso. Il costo per pezzo per la produzione a basso volume è indiscutibilmente a favore del Binder Jetting, che permette una flessibilità illimitata del prodotto a costi virtualmente nulli. Per la produzione ad alto volume, tuttavia, i costi di produzione sono ancora a favore del Metal Injection Molding. Possiamo aspettarci di trovare il punto di pareggio per i costi di produzione tra le due tecnologie tra 10.000 e 30.000 pezzi prodotti, a seconda delle caratteristiche del pezzo. Infine, un altro aspetto interessante da esaminare è il tempo di risposta alle nuove richieste. Con il Binder Jetting, i nuovi design possono essere implementati e prodotti in poche ore, mentre il MIM richiede almeno alcune settimane per la preparazione dell'attrezzatura dedicata, il che dà il vantaggio al BJT per la produzione di prototipi, pezzi di ricambio critici o, in generale, pezzi che richiedono un lead time molto basso. Ecco perché sempre più aziende MIM stanno adottando il Binder Jetting non come un'alternativa, ma come una tecnologia complementare per aiutare a coprire tutte le richieste del mercato.
Un'interessante alternativa al BJT è data dal Material Jetting (MJT), dove gocce contenenti sia il materiale di base che il legante sono selettivamente depositate insieme. Il Material Jetting per materiali metallici è una tecnologia abbastanza nuova, che al momento è stata brevettata e commercializzata solo dall'azienda israeliana XJet attraverso la loro tecnologia NanoParticle Jetting. I principali vantaggi della MJT sono legati allo spessore ultrasottile dello strato e alla conseguente alta risoluzione del pezzo, grazie alle dimensioni in nanoscala delle particelle che vengono gettate, e alla facilità di manipolazione del feedstock che, non contenendo alcun tipo di polvere sciolta, è esente da qualsiasi requisito di sicurezza particolare.
Conclusioni
Il Binder Jetting si è indiscutibilmente evoluto da una tecnologia promettente, per lo più limitata alla prototipazione, a una seria alternativa sia per le lavorazioni convenzionale che per la produzione additiva.
C'è da aspettarsi che, con la diffusione del Binder Jetting e la crescente esperienza sulla tecnologia, una conoscenza più profonda del design per BJT, i parametri di processo e l'ottimizzazione dei cicli di sinterizzazione si diffonderà nell'industria.
Nel frattempo, affidarsi a esperti dell'industria della metallurgia delle polveri e della sinterizzazione, come TAV VACUUM FURNACES, accelererà sicuramente la curva di apprendimento dei nuovi utenti del Binder Jetting, aiutandoli a trarre il massimo dalla tecnologia.
TAV VACUUM FURNACES ringrazia Cor.Sa 3D per il suo contributo a questo articolo.