I forni a vuoto consentono di ottenere un prodotto di elevata qualità e a basso costo unitario, eliminando scarti di produzione eccessivi e sprechi di materie prime. A prescindere dal settore di riferimento (automobilistico, aerospaziale, energetico, ecc.), il vuoto fornisce le condizioni ideali per il processo di brasatura dei componenti in Alluminio (lega) degli scambiatori di calore.
In questo articolo non mi limiterò a spiegare perché si dovrebbero fare brasature in vuoto, ma vi darò anche dei consigli utili sulla pulizia del forno e vi mostrerò come evitare due rischi potenzialmente pericolosi.
Come ben sapete, la brasatura è un processo che presenta aspetti delicati per la difficile disgregazione del film di ossido superficiale sul materiale di base (3003, 3105, 6951, ecc.). Ma quali sono le condizioni che hanno portato a considerare i forni a vuoto come la scelta migliore per la brasatura delle parti in Alluminio (lega)?
8 motivi per brasare sotto vuoto
- Elevato vuoto finale grazie a sistemi di pompaggio di grande portata (pompe a diffusione + pompaggio criogenico) che creano un’atmosfera residua a bassa presenza di ossigeno;
- Uso calibrato della lega a contenuto di Magnesio (4004, 4104, 4044, 4045) in modo da evitare la sublimazione del Mg in eccesso nella camera da vuoto;
- Rapido passaggio della carica, durante la fase di riscaldamento, da 520°C (temperatura di inizio sublimazione del Mg) a 605/610°C, grazie all’elevata potenza del forno. Una caratteristica che evita il ricrearsi di uno strato ossidato (Al2O3) sulla superficie del pezzo appena ridotta ad Al;
- Uniformità di temperatura della carica (± 3°C a 605°C) ottenuta attraverso la distribuzione delle zone riscaldanti e il controllo puntuale della potenza erogata;
- Adeguati sistemi di fissaggio del singolo scambiatore per evitare deformazioni o collasso del pezzo;
- Raffreddamento controllato con acqua riscaldata (80°C) delle pareti e degli altri elementi del forno per evitare la condensazione del vapore acqueo contenuto nell’atmosfera durante le operazioni di carico/scarico;
- Pulizia dei componenti;
- Nessuna emissione di sostanze contaminati nell’atmosfera.
Daremo ora uno sguardo sulla pulizia del forno a vuoto e poi vi mostrerò anche come evitare alcuni problemi di qualità.
Ti è piaciuto fino a qua l'articolo?
Prima di continuare nella lettura, seguici sulla nostra pagina Twitter cliccando il pulsante qui sotto!
In tal modo rimarrai aggiornato sulle tecnologie più avanzate per i trattamenti termici non solo con i nostri articoli, ma anche con le migliori pubblicazioni che raccogliamo in giro per la rete.
Quale ciclo di pulizia prima della brasatura?
Non mi stancherò mai di ripeterlo: i processi sottovuoto necessitano di un ambiente pulito. Il residuo dell’olio di taglio (usato per la realizzazione di piastre, turbolatori, elementi separatori, ecc.) costituisce un ostacolo al mantenimento delle condizioni ideali per il processo di brasatura: l’olio evaporato dai pezzi contamina il forno e le pompe a diffusione. Si crea così un ostacolo ad un cordone della giunzione continuo e, quindi, una difettosità.
Prima di caricare i componenti dello scambiatore di calore in forno per la brasatura sottovuoto, vi suggerisco questo ciclo di pulizia:
Componenti placcati (4004, ecc.)
- vapore a 80°C
- pulizia ad ultrasuoni
- asciugatura
Componenti NON placcati
- sgrassaggio a vapore
- soluzione acido o basica
- risciacquo in acqua
- bagno in acido nitrico
- risciacquo in acqua
- asciugatura
Eccesso di Magnesio: attenzione ai rischi!
Il forno per la brasatura dei componenti in Alluminio (lega) ha bisogno di Magnesio, MA... Una formazione eccessiva di ossido di magnesio (residui lasciati dal processo di brasatura) impedisce al forno di brasare correttamente e può dar vita a 2 situazioni potenzialmente pericolose.
- La formazione di depositi di ossido di magnesio (MgO) e magnesio (Mg) condensati su superfici fredde possono innescare un corto circuito tra resistore e schermatura riflettente della camera termica. L’ossido, infatti, crea degli ammassi di deposito fortemente ancorato e difficilmente eliminabile. Il deposito mantiene una sufficiente conduzione elettrica da rendere possibile il corto circuito. Per evitare questa situazione esistono, grazie alla continua evoluzione della conoscenza dei materiali, particolari schermature. E non solo! Oggi, l’uso del Mg come getter atto a migliorare il vuoto limite durante il processo ha trovato una soluzione alternativa nell’utilizzo del pompaggio criogenico, che elimina le tracce di vapore acqueo residuo dal lavaggio dei materiali stessi.
- I depositi di Magnesio (Mg) possono innescare una situazione altamente pericolosa durante la loro rimozione. In presenza di aria (situazione che si verifica quando l’operatore cerca di eliminarli) il magnesio si accende con estrema facilità e brucia formando gocce a 2000°C che non si possono estinguere con l’acqua e che possono provocare gravi lesioni all’operatore.
E voi... Utilizzate ancora polvere o pastiglie di Magnesio per la brasatura dei componenti in Alluminio (lega) degli scambiatori di calore?
Ti è piaciuto l'articolo?
Iscriviti al nostro canale Telegram, in tal modo potrai restare aggiornato sulle tecnologie più avanzate per i trattamenti termici.
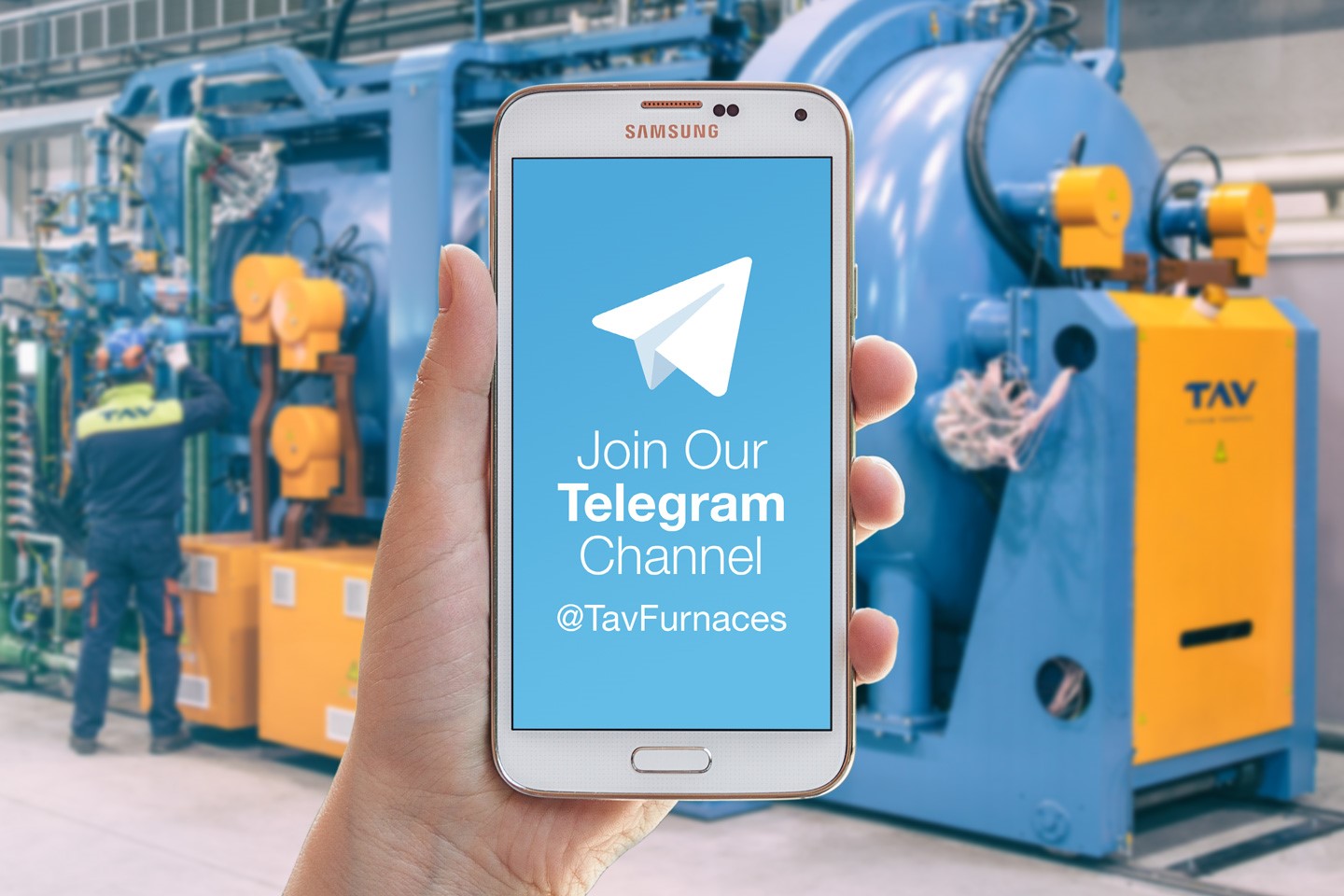
Non hai Telegram?
Se ancora non hai Telegram, usa uno dei seguenti pulsanti per installarlo:
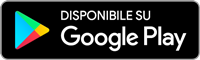
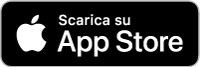