A key to keeping your vacuum furnace running well is your maintenance strategy. There are two main types of maintenance strategies: preventive maintenance and predictive maintenance. In Part 1 of the article, I addressed topics related to preventative maintenance – I discussed maintenance role in keeping performance efficiency, quality products, on-time deliveries, environment and safety requirements, and total plant cost effectiveness.
In Part 2 of the article, I will focus on predictive maintenance (PdM), which offers a whole host of advantages over its more basic relative preventive maintenance, because it responds to the actual status of equipment instead of relying on pure averages. In practical terms, PdM uses condition monitoring vacuum furnace to detect when repairs should be made. Let us examine this powerful tool, by learning why and how it can be so valuable for your vacuum furnace.
Predictive Maintenance (PdM): how does it work?
Predictive maintenance is maintenance that directly monitors the condition and performance of vacuum furnace during normal operation to reduce the likelihood of failures. PdM attempts to keep costs low by reducing the frequency of maintenance tasks, reducing unplanned breakdowns, and eliminating unnecessary preventive maintenance.
Basically, predictive maintenance differs from preventive maintenance by basing maintenance needs on the actual condition of the furnace, rather than on some predetermined schedule. Recall that preventive maintenance is time-based. Activities such as changing lubricant are based on time, like calendar time or equipment run time. No concern is given to the actual condition and performance capability of the oil. It is changed because it is time. With predictive maintenance, instead, you consistently monitor and test lubrication conditions.
Predictive maintenance evaluates the condition of equipment by performing periodic or on-line asset condition monitoring. Most PdM is performed while vacuum furnace is operating normally to minimize disruption of everyday operations. This maintenance strategy leverages the principles of statistical process control to determine when maintenance tasks will be needed in the future. PdM uses real-time data gathered from furnaces to notify you when something is starting to go wrong. This method goes beyond calendar-based maintenance, using the actual condition of the vacuum furnace to determine when repairs are performed.
Predictive maintenance survives on trend values and relevant analysis. PdM algorithms are based on the data provided by diverse condition-monitoring tools as vibration and oil analysis. Comparing the expected vacuum furnace’s behavior and its gradual deterioration, PdM identifies trends and determines when a piece of equipment needs a special attention.
Cost benefits of predictive maintenance
Employing a condition monitoring solution that tracks furnace pressure, temperature, and humidity levels is the most effective predictive maintenance strategy, because it covers critical functions:
- Provides real-time and historical data trends of vacuum furnaces and processes;
- Allows operators to detect and diagnose any issues that could snowball into problems;
- Delivers analytics and alerts to operators when needed.
Maintaining your vacuum furnace is most cost-effective if done when it is needed. To that end, PdM systems are designed to ensure that servicing doesn't happen too soon, wasting money on unnecessary work, or too late, after wear and time have caused undue deterioration. PdM systems can also help plan an inventory for replacement parts and provide input on vacuum systems that need a design upgrade because of unacceptable performance.
By combining asset management and analytics solutions, you can achieve more robust operational flexibility and fewer disruptions, and reap the proven benefits of predictive maintenance, the full contents of which are set forth below:
- Reduced equipment and labor costs – Instead of replacing an entire piece of equipment due to a breakdown, a repair is made prior to failure and cost is minimized to the price of each component. Moreover, the number of repair activities will be greatly reduced and less labor is needed to attend to faulty equipment;
- Reduced lost production time – Predictive analytics helps you reduce unplanned production downtime by allowing better maintenance scheduling. It means you can maximize uptime and head off critical failure downtime by scheduling repair during non-productive times;
- Increased safety – Predictive maintenance would allow potential problems to be fixed before failure occurs, which would create safer conditions for operators and users;
- Increased revenue – With less maintenance on good components and quicker repair of faulty components, repairs can be more effectively handled, thereby reducing repair time;
- Increased wrench time – By identifying the precise repair task needed to correct deficiencies, as well as the parts, tools and support needed to correct the problem can dramatically increase the productive time technicians spend actually repairing or replacing equipment.
Having learned how predictive maintenance can effectively reduce your maintenance costs, the time has now come to see what instrument and devices to use, in order to ensure the lifespan and reliability of your vacuum furnaces and processes by identifying problems before they occur.
Did you like this article up to here?
Before you continue, follow us on our LinkedIn page pressing the button here below!
In this way, we'll be able to keep you updated on most advanced technologies for heat treatments not only with our posts, but also with the best articles that we collect around the web.
Smart tools for predictive maintenance
Predictive maintenance helps you assess vacuum furnaces, diagnose problems using monitoring tools like sensors and image analytics, design the appropriate solution leveraging advanced algorithms and machine learning principles, and deploy an optimized furnace lifecycle maintenance plan.
Predictive maintenance helps you identify the optimum junctures for maintenance work and, above all, avoid lost production time. The beauty of most of the PdM tools is that they require vacuum furnace to be running at normal capacity and do not interfere with your production schedules.
There are many different predictive maintenance tools and techniques available today. Choosing the best nondestructive testing technique depends on the company’s needs and the type of furnaces an organization employs. Here are a few common diagnostic tools used in predictive maintenance:
- Infrared thermography analysis – Without disrupting productivity, an infrared imager evaluates the temperature profile of a piece of equipment to keep it from overheating and failing.
- Sonic/ultrasonic analysis – These instruments convert the frequencies an asset is making into auditory or visual signals to be evaluated. The frequencies measured are generated from furnace issues like faulty electrical equipment, leaky valves, unlubricated bearings, etc.
- Vibration analysis – In its simplest form, vibration analysis is a measurement of displacement over time. By measuring displacement, velocity or acceleration, you can get insight into bearing failures, imbalance, misalignment, wear, looseness, etc.
- Oil analysis – This checks the lubrication of an asset. Oil analysis can be broken down into three main categories: lubricant’s health, vacuum furnace’s health and contamination. Every test performed on an oil sample can be categorized in at least one of these areas.
Predictive maintenance uses condition-monitoring instruments to evaluate a vacuum furnace’s wear and efficiency in real-time. Part of any strong PdM program is the ability to verify a fault with more than one technology. This not only ensures the validity of the fault but also helps make a more accurate and precise repair recommendation. The importance of verification with additional diagnostic tools is never more evident than on a critical piece of equipment that requires furnace outages for repairs.
What is the value of a proactive maintenance strategy?
When it comes to maintenance strategy, you are either taking a reactive approach or a proactive one. The simplest maintenance strategy is that of “breakdown maintenance”. When failure occurs, reactive maintenance is performed to fix the equipment and return it to full operation. But this “run-to-failure” approach can be extremely costly because:
- Shutdowns happen during production runs;
- Expedited shipping for spare parts costs much more than regular shipping;
- Maintenance staff is often forced to work overtime to repair machinery.
I think, it is time to leave reactive maintenance behind in order maintain the reliability of vacuum furnaces. On this point, it has been proven that proactive strategies can improve a facility’s bottom line in many ways: lowering maintenance costs, improving asset reliability and giving a 360-degree view of performance, just to name a few.
Sudden machine failures can result in contract penalties and lost revenue, and can even ruin the reputation of a business. The purpose of proactive maintenance is to view vacuum furnace failure and similar problems as something that can be anticipated and dealt with before they occur. Proactive maintenance consists of preventive maintenance and predictive maintenance.
Proactive maintenance is the maintenance attitude that supplants “failure reactive” with “failure proactive” by activities that avoid the underlying conditions that lead to vacuum furnace faults and degradation. Adoption of proactive maintenance strategies can result in substantial cost savings and higher furnace reliability.
I personally believe that good maintenance begins with a proactive approach to maintain and protect vacuum furnaces of all kinds. Speaking of which, it would be nice if you would share your opinion with us. Is your maintenance strategy reactive or proactive? And why?
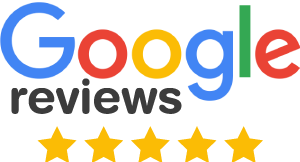
Do you like this blog?
For us your opinion matters, so we would be very pleased if you could write a review about us or our blog.